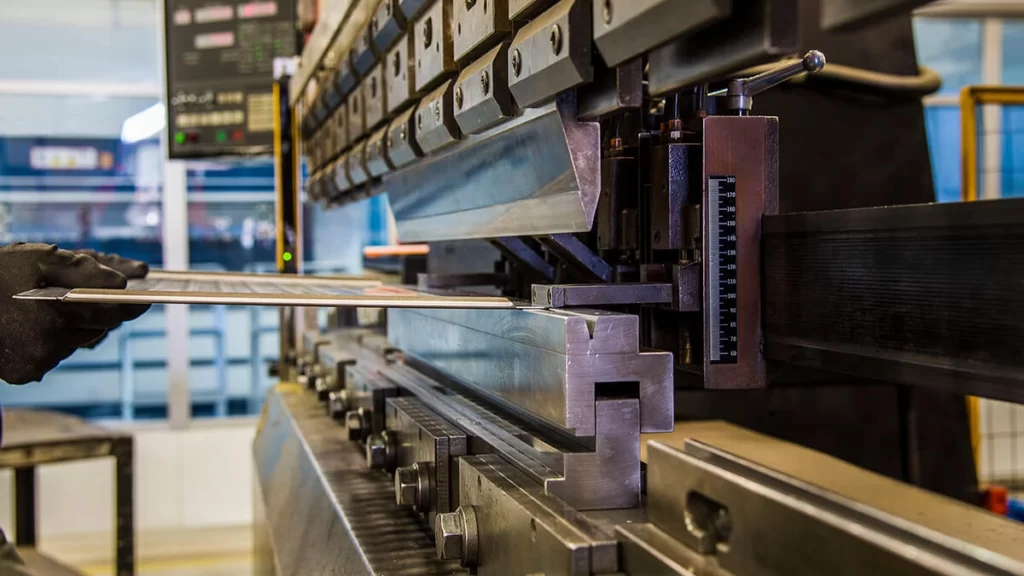
Introduction
The press brake is a vital tool in metal sheet fabrication, serving the crucial role of achieving precise bending and forming. Widely used in precision machinery industries like automobile manufacturing and aerospace, it ensures product precision and production efficiency. However, the common issue of the press brake not going up troubles many sheet metal enterprises, causing production delays, delivery issues, and impacting workpiece quality. This guide aims to provide a comprehensive solution by exploring various reasons for the press brake malfunction and offering insights from equipment maintenance to malfunction troubleshooting.
I. Understanding Press Brakes
Basic Components of a Press Brake The press brake consists of fundamental components: body frame, hydraulic system, electric control system, back gauge device, tooling (upper punch and bottom die), and worktable. The body frame provides the basic structure, the hydraulic system exerts bending pressure, and the electric control system ensures precision and automation. The back gauge positions the sheet, tooling shapes the workpiece, and the workbench supports and fixes the sheet.

How Press Brakes Function in Metal Fabrication In metal fabrication, press brakes, assisted by hydraulic pressure, precisely bend flat metal sheets into 2D or 3D shapes by adjusting the angle and distance between the upper and bottom die. This process is crucial for manufacturing various sheet metals such as boxes, shells, and brackets.
Significance of Press Brake Maintenance The press brake’s stability and lifespan hinge on daily maintenance practices. Regular lubrication, cleaning, and component checks prevent malfunctions caused by aging, abrasion, or blockages. Maintenance habits ensure precision, reduce errors, improve production quality, prolong equipment lifespan, and minimize downtime and costs.
II. Common Issues in Press Brake Operations
Overview of Common Press Brake Problems Various problems plague press brake operations, including precision errors, tooling wear, and electrical malfunctions affecting the back gauge’s accuracy. This guide focuses on a common situation—the press brake not going up. This issue halts the entire sheet metal processing, severely impacting production efficiency and quality.
Initial Diagnosis: Steps to Assess the Problem For an initial diagnosis of the press brake not going up, operators should follow these steps:
- Check hydraulic system oil level, leaks, or blockages.
- Ensure smooth power supply and signal transmission in the electrical control system.
- Observe abnormal noise or vibration to identify potential mechanical component damage or blockage.
Mechanical vs. Electrical Issues The “press brake won’t go up” issue may stem from mechanical or electrical problems. Mechanical problems involve worn or blocked components like hydraulic cylinders, pistons, and seals. Electrical issues arise from failures in controllers, motors, sensors, or power supply lines.
Safety Precautions Safety is a priority in press brake troubleshooting. Operators must adhere to working regulations, using specialized tools and setting warning signals before repairs to avoid accidents.
III. Mechanical Causes and Solutions
Hydraulic System Malfunctions
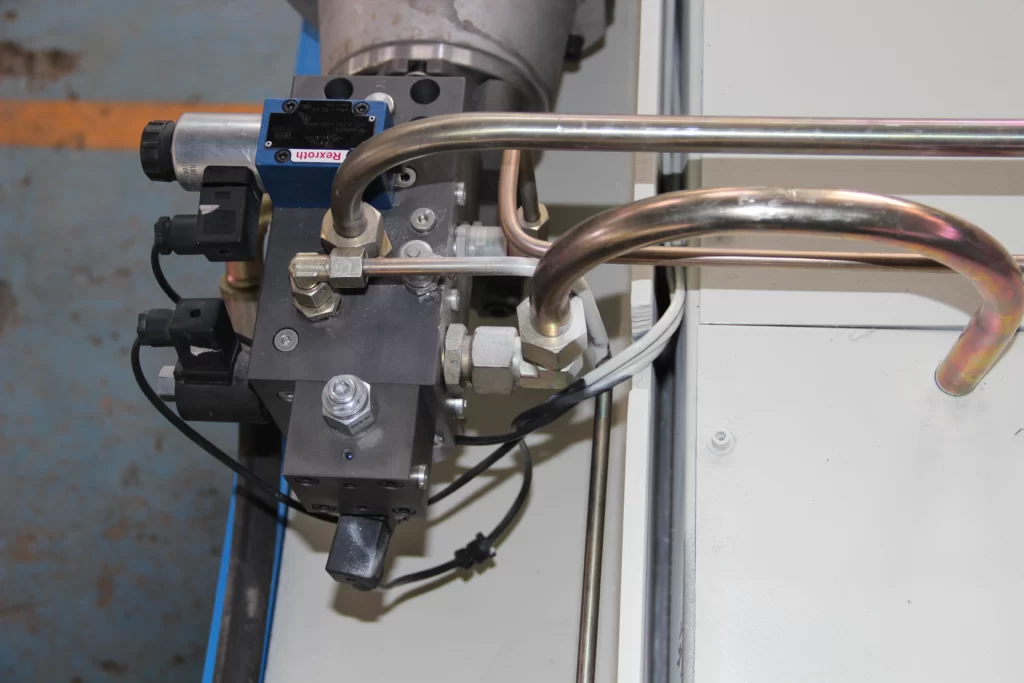
- Hydraulic oil leakage: Regularly check and replace worn or damaged seals to prevent leaks.
- Hydraulic pump: Inspect and replace pump components to maintain proper pressure.
- Blocked hydraulic line: Ensure regular cleaning to maintain smooth fluid flow.
Mechanical Failures
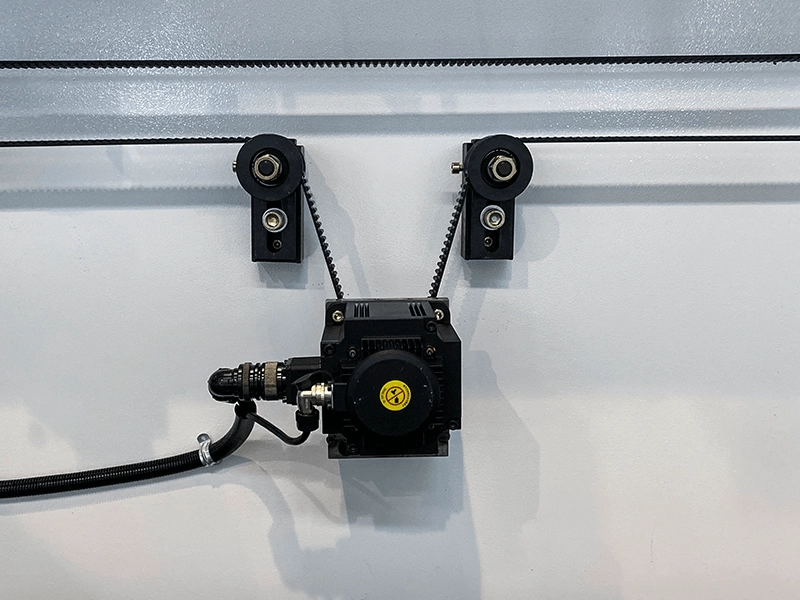
- Bending rod problem: Regularly check and replace worn bending rods to ensure accurate bending.
- Ram and guide rail failure: Lubricate and inspect the ram and guide rail regularly to prevent blocking or misalignment.
- Electrical component failure: Check electrical system connectivity and status regularly to ensure normal operation.
Regular Maintenance Tips
- Checking regularly: Establish a routine for checking mechanical and electrical systems to identify problems early.
- Cleaning and lubricating: Regularly clean and lubricate hydraulic systems and mechanical components to prevent friction.
- Operator training: Ensure operators receive proper training to recognize normal machine movement and potential failure situations.
IV. Electrical Causes and Solutions
Electrical Component Failures
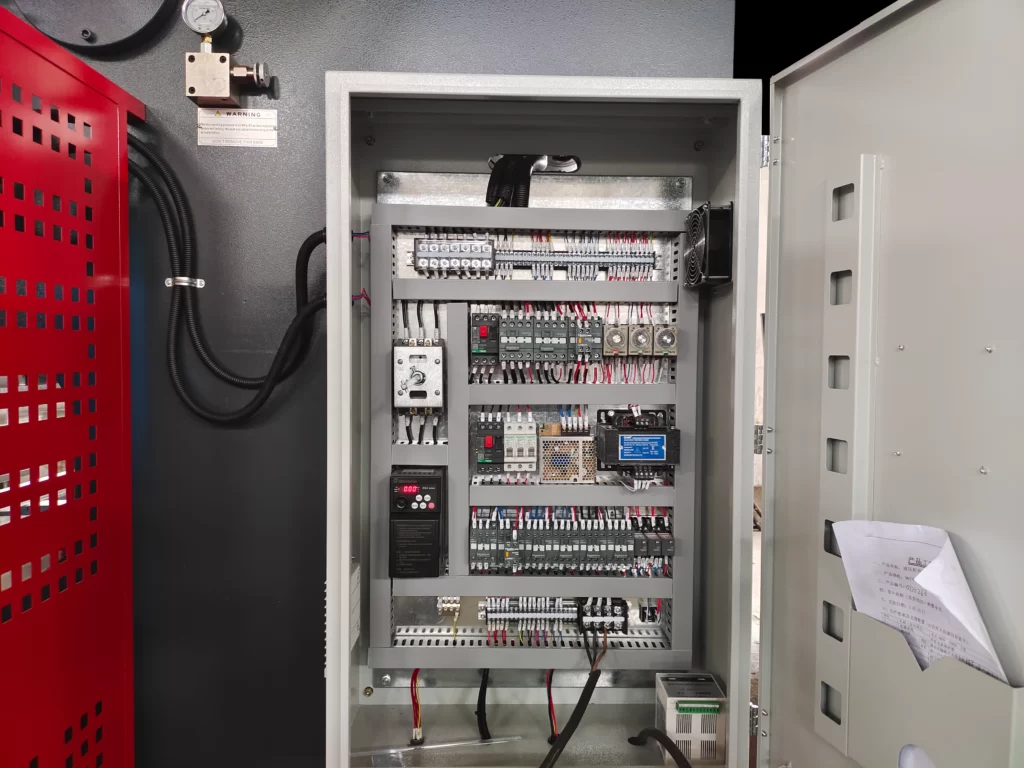
- Cable and wiring issues: Inspect cables for damage and ensure secure connections.
- Electrical components aging: Replace aging components like relays and switches.
- Power problems: Ensure stable power supply and use protective equipment to prevent overloads.
Troubleshooting Electrical Issues
- Shut down and ensure safety: Cut off power before addressing electrical issues to ensure operator safety.
- Preliminary judgment: Identify potential trouble areas based on observed failures.
- Detailed checking: Inspect connectors, cables, switches, relays, and other components.
- Test and verify: Use test tools to confirm the source of the failure.
- Repair and replace: Timely repair or replace damaged electrical components to restore normal operation.
Preventative Electrical Maintenance
- Checking regularly: Establish a plan for checking electrical components regularly.
- Cleaning and maintenance: Keep electrical components clean to avoid debris accumulation.
- Electrical training: Provide basic electrical training for operators to address common electrical issues.
V. Software and Control System Errors
Identifying Software-Related Issues
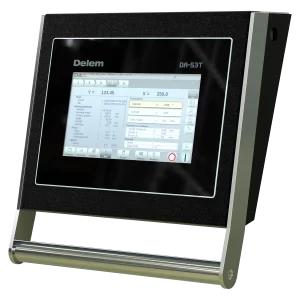
- Abnormal operation interface: Anomalous display or false information indicates software problems.
- Control system reaction: Slow or non-responsive control systems signal software failure.
- Output instability: Unstable bending angles or sizes may result from software or control system issues.
Resetting and Updating Control Systems
- Reset the system: Power down, wait, and reset to clear instant problems.
- Update the software: Check for available upgrades to fix known problems.
- Restore default settings: If issues persist, restore the control system to factory default settings.
When to Seek Professional Help for Software Problems
- Problems persist: Consult manufacturers or professional support if issues remain unresolved.
- Safety concerns: If software problems threaten safety, seek professional assistance immediately.
- Authorized maintenance personnel: Connect with authorized maintenance or technical support for complex software or control system problems.
VI. Advanced Troubleshooting Techniques
Using Diagnostic Tools
- Hardware diagnostic tools: Employ tools like oscilloscopes, multimeters, and thermal imaging cameras to measure electrical parameters and check circuit movement.
- Software diagnose systems: Utilize internal malfunction diagnose software in modern press brakes to monitor and record false codes for quick issue localization.
- Internet and communication diagnose tools: Check communication links using specialized internet tools for digital control systems.
- Remote diagnose service: Access remote diagnose functions in high-tech equipment for precise issue positioning by manufacturing technique teams.
Consulting Technical Support
- Complex questions: Seek support from manufacturing technique and professional maintenance personnel for intricate problems.
- Under warranty: If under warranty, consult the manufacturer for assistance.
- Safety questions: For safety-related concerns, stop equipment immediately and seek professional help.
- Professional advice: If problems persist, consult professional support for advice and solutions.
VII. Conclusion
This guide extensively covers press brake troubleshooting and performance optimization, emphasizing common issues and solutions in hydraulic, mechanical, electrical, and software systems. By maintaining equipment and enhancing operator skills, downtime can be minimized, repair costs reduced, and stability and competitiveness improved. Investing in maintenance and training is key to ensuring the successful operation of press brakes and sheet metal equipment. Visit the MACHNIST official website for information and machine purchases.