Troubleshooting Reasons Why the Blade Doesn't Rise on Hydraulic Shearing Machines
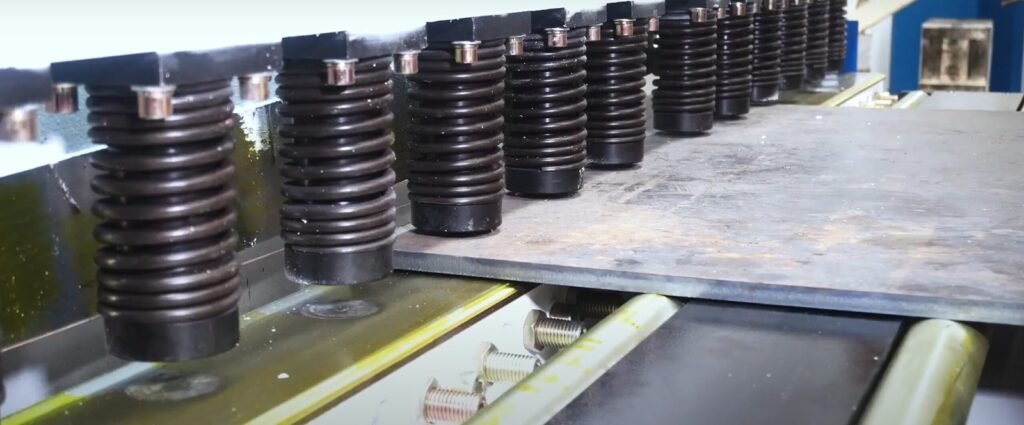
The reason of hydraulic shearing machine blade not back is mainly hydraulic system failure and debris blockage caused.
But in this blog ensures each aspect of the troubleshooting process for the hydraulic shearing machine is clearly outlined.
Covering electrical systems, control systems, transmission mechanisms, mechanical structures, and hydraulic system faults, nitrogen pressure, etc.
I will teach you step by step how to troubleshoot the problem and come up with a solution.
Electrical Faults:
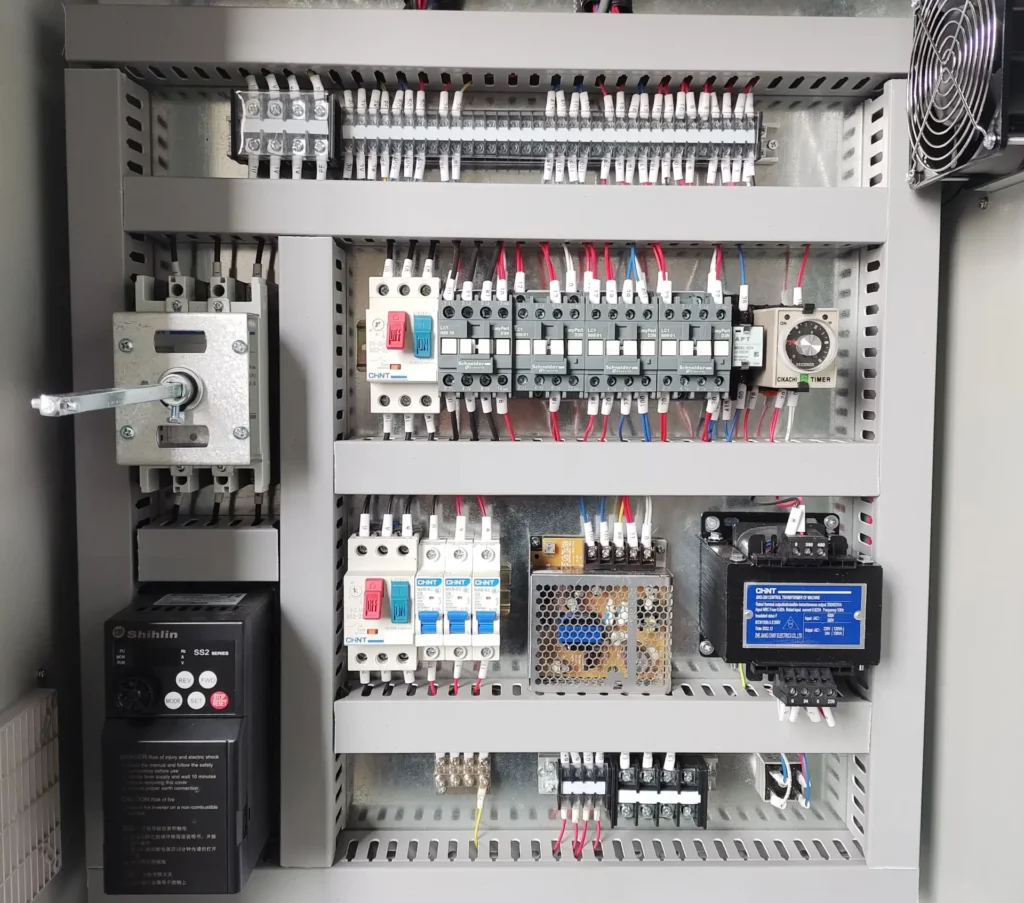
Firstly, it’s crucial to inspect the shearing machine’s power supply and control system to ensure they are operational without any faults. Common electrical system failures include motor damage, controller malfunctions, and sensor failures. Verify correct operation of the motor and oil pump in terms of forward and reverse rotations.
-
- Two-position four-way solenoid valve: If stuck, remove and clean it. Note: If the blade is down, release the pressure before removing the valve.
-
- Directional valve: If it can descend but not rise, consider replacing it. If absent, interchange the coils controlling the downward and upward directions to diagnose coil failure.
-
- Check if the up indicator light for the rising valve is illuminated.
Nitrogen Supply Check:
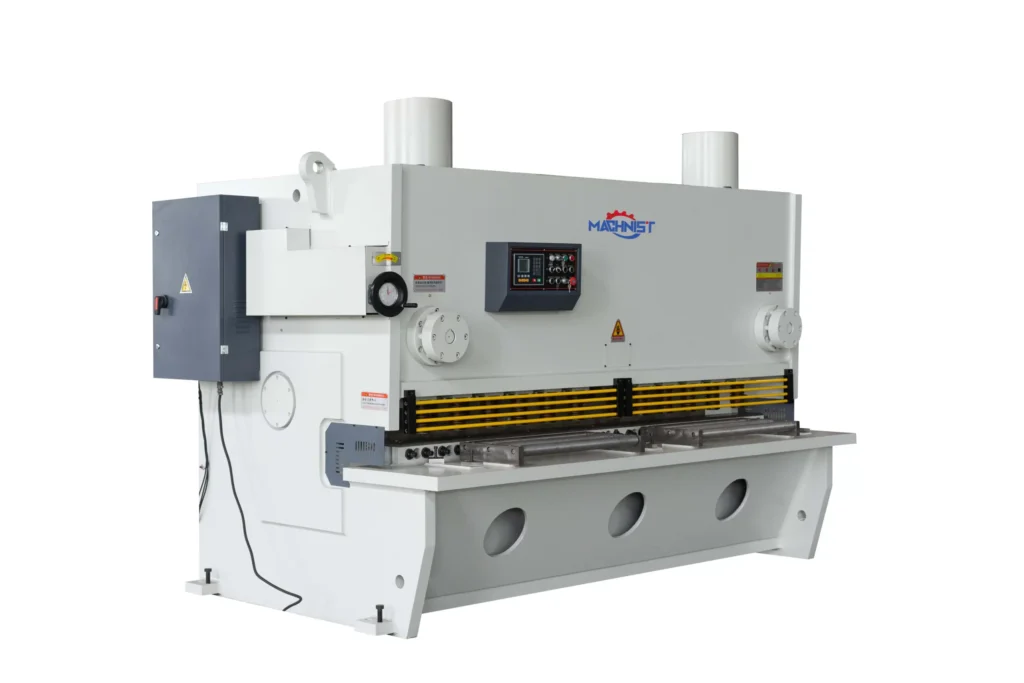
- If the shearing machine fails to rise after cutting down, start by verifying the air supply. Check the air pressure gauge;
- if pressure is low, adjust the air supply to increase pressure (recommended up to 6 MPa). Typically, leaks in nitrogen cylinders stem from aging seals, necessitating seal replacement.
- Each potential issue needs to be systematically diagnosed and repaired. It also introduces precautions and preventive measures during maintenance to enhance machine productivity and longevity.
Hydraulic System in Hydraulic Shearing Machines:
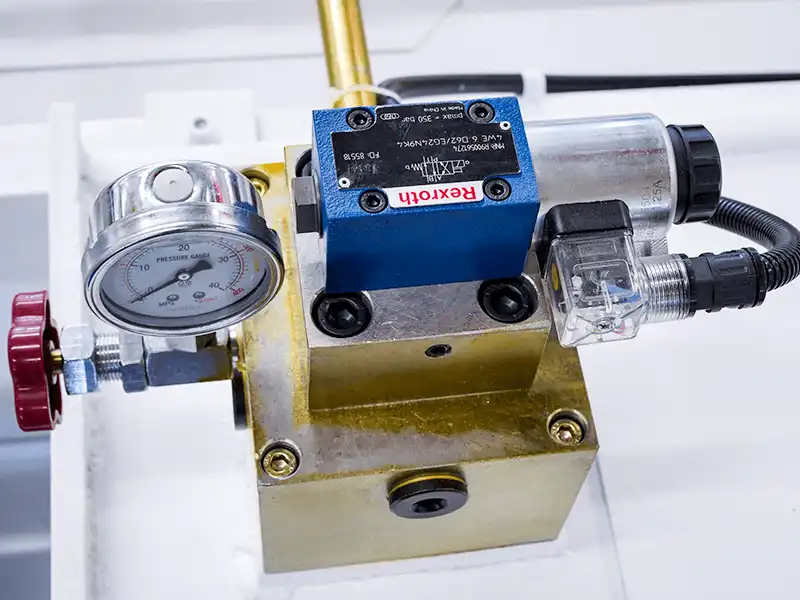
Overview:
One of the primary reasons for the blade getting stuck and not rising in hydraulic shearing machines is hydraulic system failure. The hydraulic system forms the foundation of these machines’ operation; thus, any malfunction can prevent the blade from ascending. Potential faults include throttle valve/proportional valve issues, pump failures, cylinder leaks, and clogged hydraulic lines.
1. Replacing Hydraulic Seals in Hydraulic Shearing Machines:
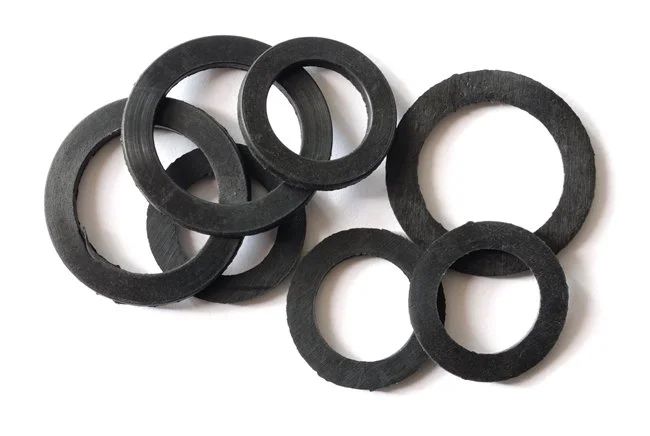
-
- Lower the blade frame of the hydraulic shearing machine to its lowest point.
-
- Cut off the power supply to the machine, then loosen and remove the damaged seal from the leaking part.
-
- Apply a layer of grease inside the joint groove, place the new seal in the groove, tighten the joint, and finally refill and reset the hydraulic shearing machine for normal operation.
2. Severe Wear of Main Relief Valve:
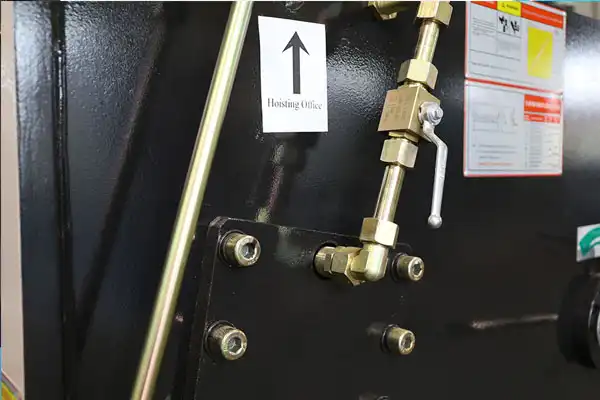
This can cause overflow and debris blockage, resulting in inadequate pressure buildup.
3. Filling Valve:
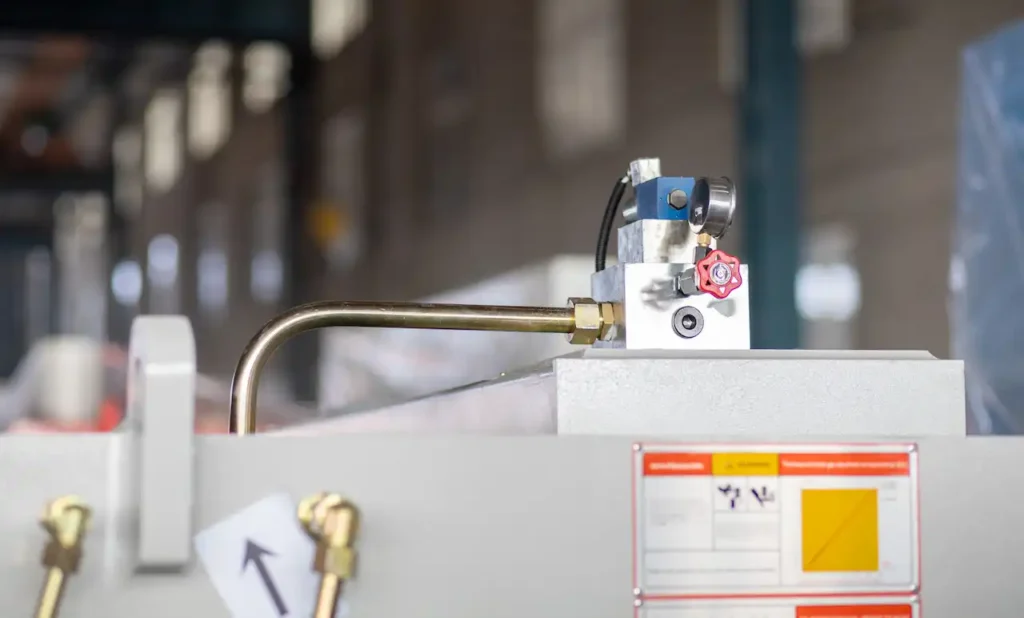
- Ensure it’s open; obstruction by debris or a spring can cause the valve core of the hydraulic system’s filling valve to jam.
- During hydraulic shearing machine disassembly, check for proper installation and mating of the cone valve or if it’s missing from the valve seat hole.
- Clean the valve core of the safety overflow valve.
Other Components of hydraulic
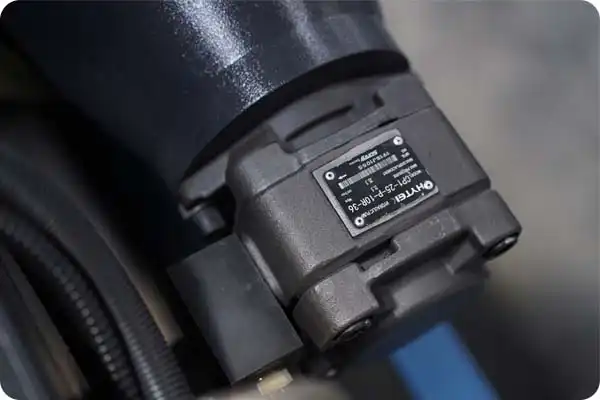
-
- Oil Pump: Flow inversely proportional to pressure can also prevent hydraulic rise.
-
- Cylinder Issues: Faults like internal wear or cylinder body rupture require inspection and subsequent replacement or repair of hydraulic cylinder components.
Mechanical Component Faults:
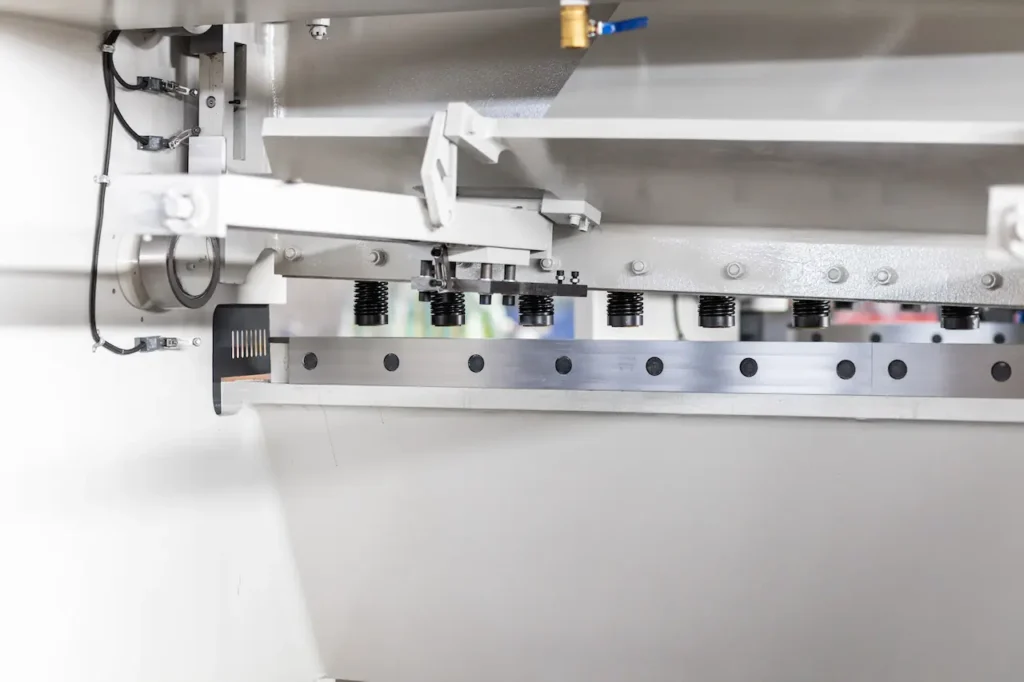
Another reason the blade might fail to rise on hydraulic shearing machines is mechanical component failure. These components include the frame, guide rails, swing arms, and knife seats.
Issues such as frame deformation, overly tight guide rails, worn swing arms, or loose knife seats can hinder blade ascent. The solution involves disassembling the hydraulic shearing machine, inspecting each mechanical part, and replacing or repairing the faulty components.
Blade Inspection:
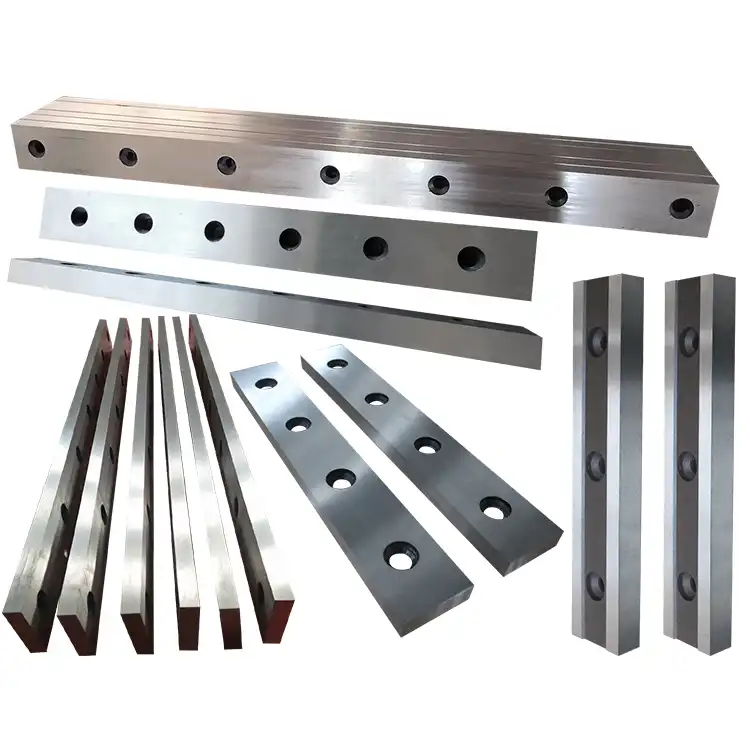
-
- Check the lower blade plate.
-
- The lower blade plate is crucial during shearing. Ensure it’s securely clamped with the upper blade and inspect for wear or deformation.
Blade Inspection:
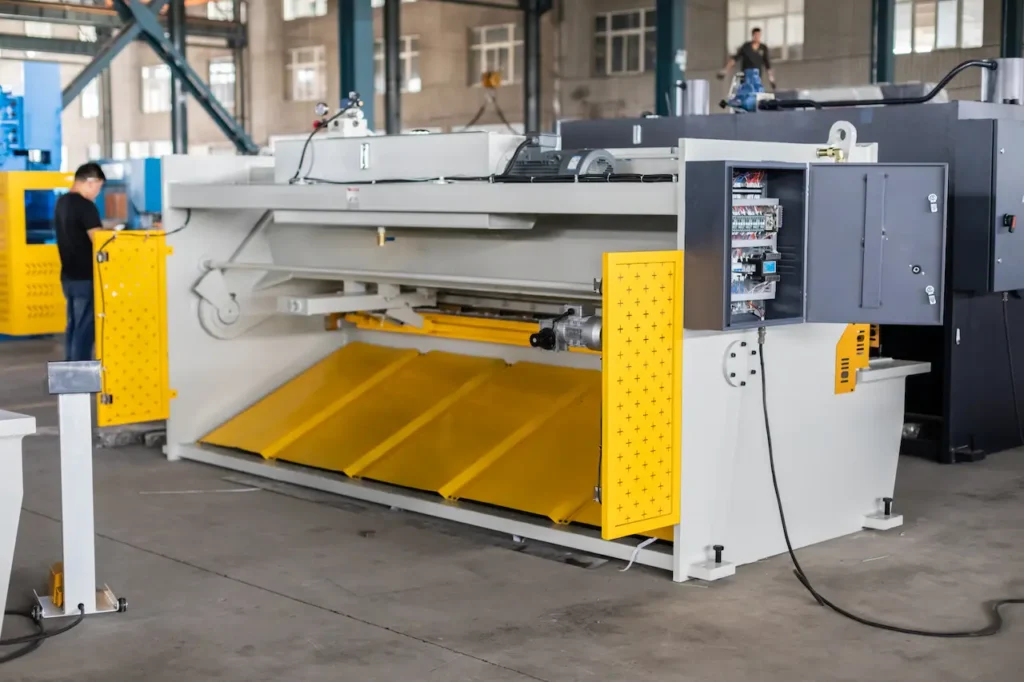
-
- Check the lower blade plate.
-
- The lower blade plate is crucial during shearing. Ensure it’s securely clamped with the upper blade and inspect for wear or deformation.
Blade Replacement:
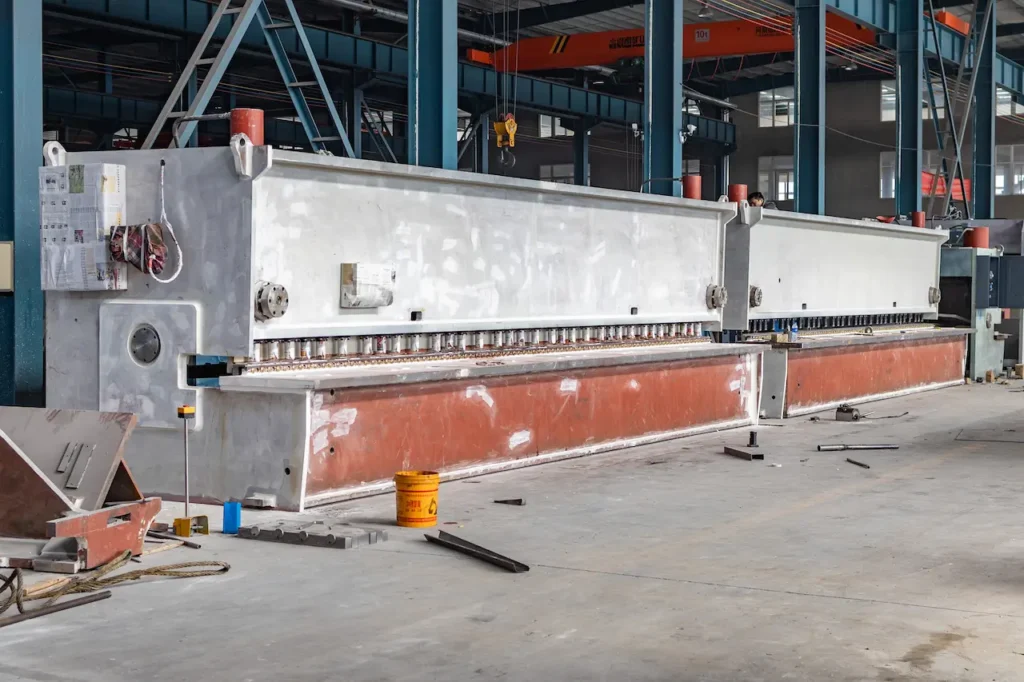
-
- If the hydraulic shearing machine’s blade fails to rise, it could indicate damaged or excessively worn blades. The replacement procedure involves:
- Power off and lock the workbench before blade replacement.
- Open the side latch of the hydraulic shearing machine and remove the blade.
- Inspect the new blade for damage or scratches, then install it.
- Reassemble the side latch of the hydraulic shearing machine to complete the reassembly.
Lubrication Deficiency:
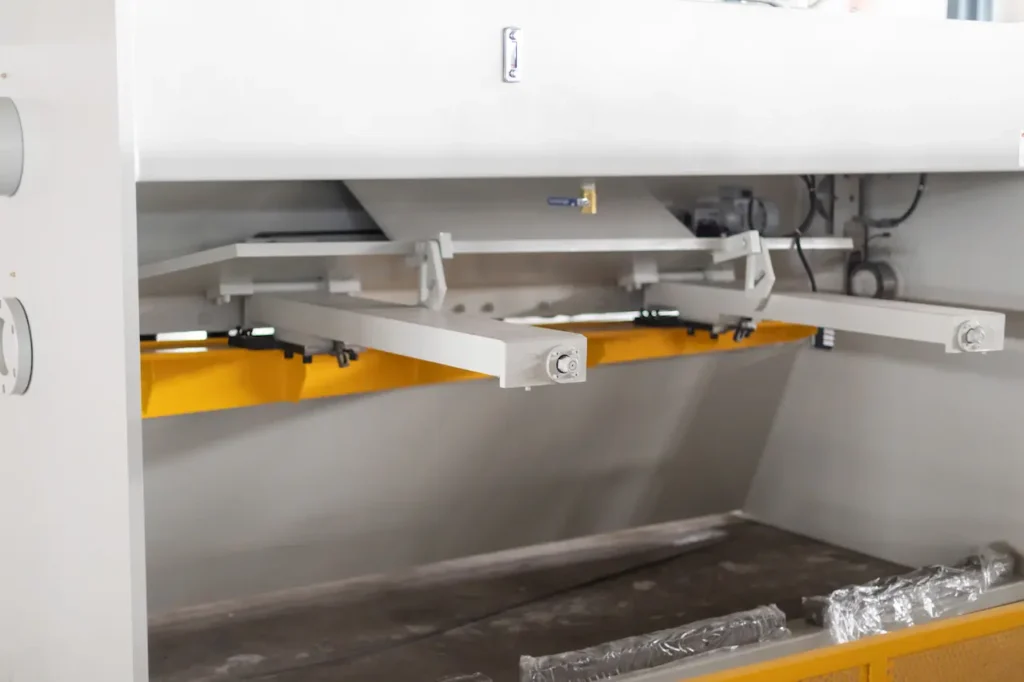
- Operation of the hydraulic shearing machine requires sufficient lubrication oil support.
- Lack of lubrication can cause hydraulic system failure, preventing blade ascent and descent. Therefore, regular lubrication oil refills are essential.
Extended reading-More knowledge about hydraulic shears
Hydraulic Shearing Machine Definition
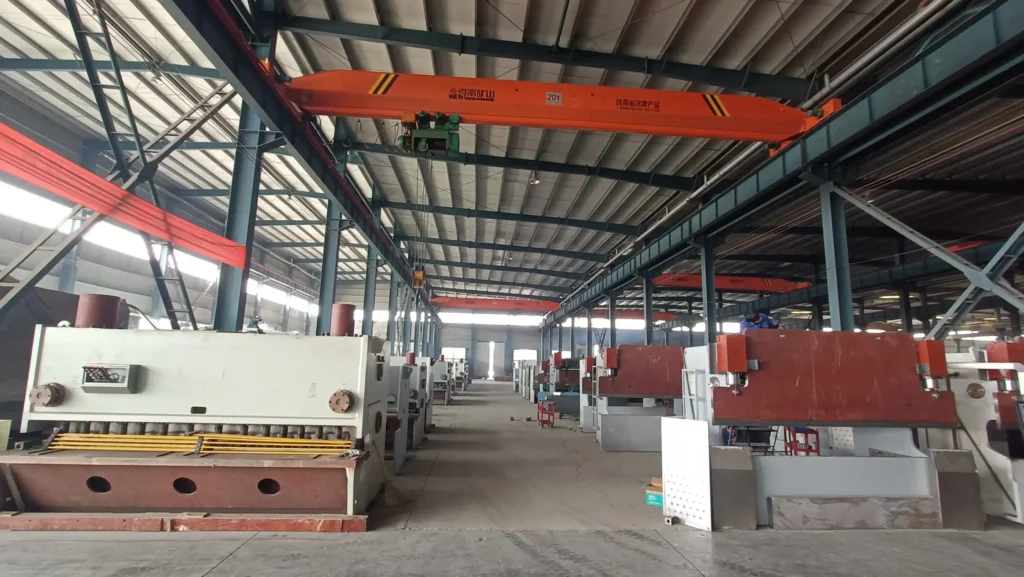
- A hydraulic shearing machine is a specialized industrial tool designed for cutting various types of sheet metal with precision and efficiency.
- It utilizes hydraulic power to drive a movable blade assembly, which applies a shearing force to the metal workpiece, resulting in clean, straight cuts.
Key Features and Components:
-
- Hydraulic System: The heart of the machine, consisting of hydraulic pumps, cylinders, valves, and hoses, which generate and control the hydraulic force needed for cutting.
- Blade Assembly: Typically comprises upper and lower blades, which are mounted on a moving ram and stationary bed, respectively. The blades are designed to shear the metal by moving past each other with a high degree of accuracy.
- Backgauge: An adjustable gauge or fence that assists in positioning the metal workpiece accurately for consistent cuts, improving overall cutting precision.
- Control System: Incorporates electronic controls or manual interfaces to operate the machine, adjust cutting parameters, and monitor cutting processes for safety and efficiency.
- Safety Features: Includes safety guards, emergency stop buttons, and interlocking mechanisms to ensure operator safety during machine operation.
Introduction of two different type of hydraulic shearing machine:
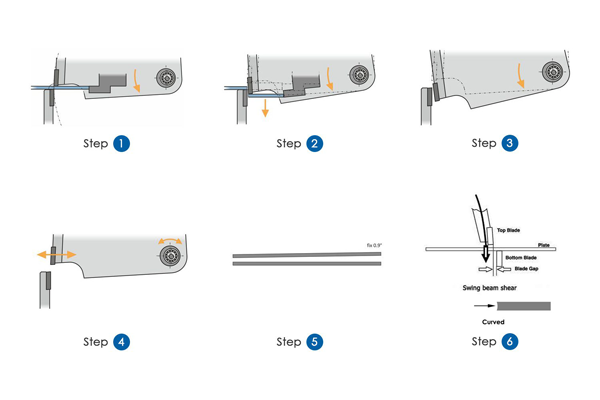
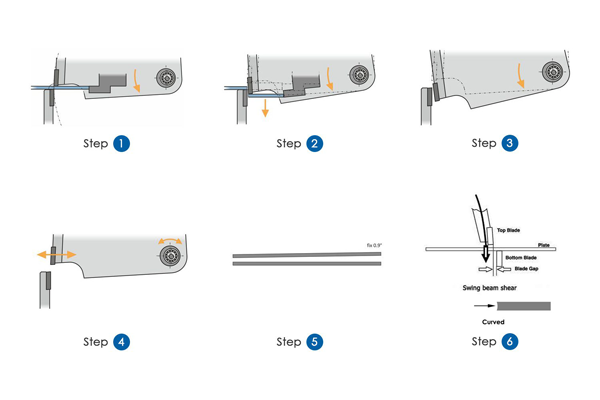
- the hydraulic swing beam shearing machine and the hydraulic guillotine shearing machine.
- Each type offers distinct advantages depending on the specific requirements of metal sheet cutting applications.
Working Principles Comparison: Hydraulic Swing Beam Shearing Machine vs Hydraulic Guillotine Shearing Machine
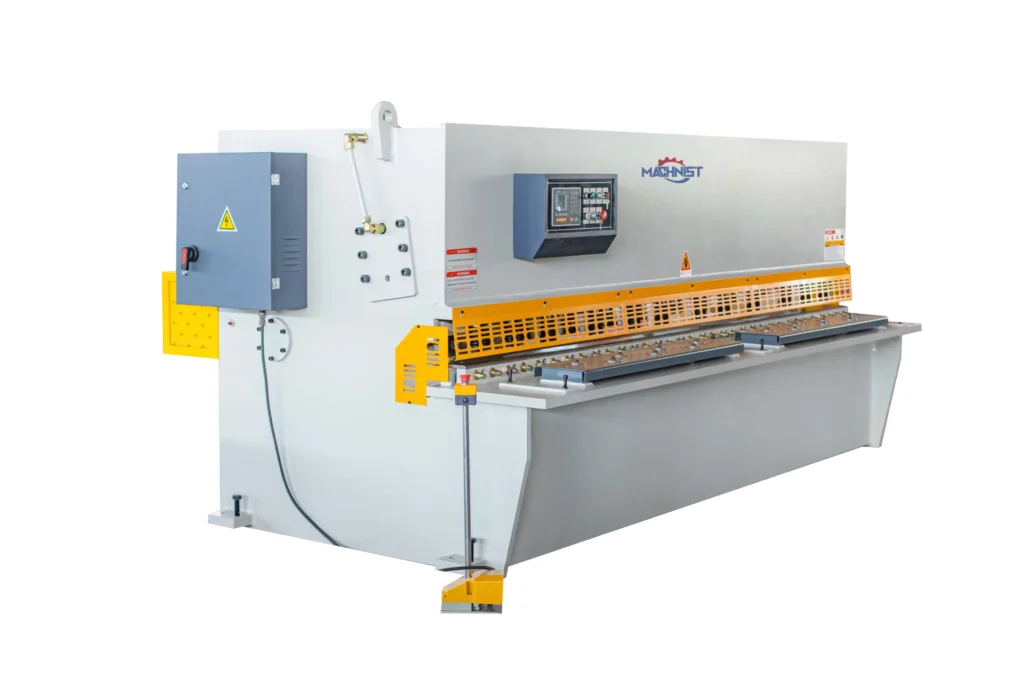
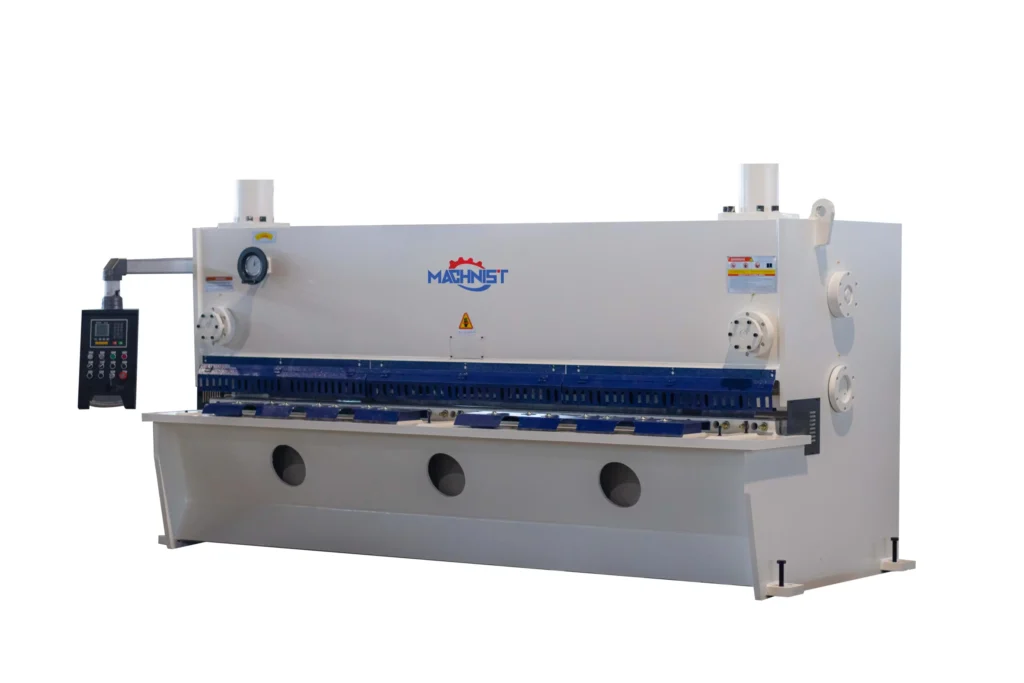
Hydraulic Swing Beam Shearing
-
- Hydraulic System Drive: The hydraulic swing beam shearing machine operates using a hydraulic system comprising components such as hydraulic pumps, cylinders, and valves.
- Cutting Action: During operation, the operator places the metal sheet to be cut on the machine’s worktable. The hydraulic system controls the hydraulic oil flow into and out of the cylinder, moving the upper blade downwards or upwards.
- Cutting Process: The upper blade applies downward force through the hydraulic cylinder, clamping the metal sheet with the fixed lower blade. Once clamped, the upper blade swiftly descends, shearing the metal sheet against the fixed lower blade.
- Control and Adjustment: Equipped with an electronic control system or manual interface, operators can adjust cutting parameters such as blade clearance and cutting speed to accommodate different thicknesses and hardnesses of metal sheets.
- Safety Features: The machine is typically equipped with safety devices like protective covers and emergency stop buttons to ensure operator safety during operation.
Hydraulic Guillotine Shearing Machine
- Blade Motion: The hydraulic guillotine shearing machine employs a different blade structure, typically controlled by the hydraulic system to open and close the blades.
- Blade Movement: The blades of the guillotine shearing machine are controlled by hydraulic cylinders, moving along a straight line to clamp and shear the metal sheet against the lower blade.
- Cutting Force Control: The hydraulic system controls the opening and closing of the blades, ensuring sufficient force is applied through the hydraulic cylinders to achieve clean cuts on the metal sheets.
- Applications: Guillotine shearing machines are suitable for applications requiring precise and stable cutting actions, particularly for tasks demanding strict dimensional accuracy.
- Operation and Adjustment: Similar to the swing beam shearing machine, it features an electronic control system or manual interface for operational adjustments and monitoring during cutting processes
Application of Hydraulic Shearing Machines
- Hydraulic shearing machines are widely used in various industries for cutting sheet metal and other materials efficiently. They are essential in:
- Metal Fabrication: Hydraulic shearing machines are crucial in metal fabrication shops for cutting large sheets of metal into smaller sizes with precision.
- Automotive Industry: They play a significant role in manufacturing processes within the automotive industry, particularly in the production of vehicle components and body panels.
- Construction: Hydraulic shearing machines are used in construction for cutting metal sheets used in building structures and other construction materials.
- Shipbuilding: In shipyards, these machines are used to cut metal sheets for constructing ship components and hulls.
- Aerospace Industry: They are utilized in the aerospace sector for cutting metal sheets and components used in aircraft manufacturing.
- General Manufacturing: They find application in various manufacturing processes where precise cutting of metal sheets is required, such as in appliance manufacturing and electronics.
- Scrap Recycling: Hydraulic shearing machines are also used in recycling facilities to process scrap metal efficiently.
- These machines offer high cutting precision, ease of operation, and reliability, making them indispensable in modern industrial operations
Derivative reading 2
Blade material and processing technology
Hydraulic shearing machines are vital tools in the metalworking industry, used extensively for cutting sheet metal with precision and efficiency.
Central to their functionality are the blades, which play a crucial role in determining the quality and effectiveness of the cutting process.
This article explores the materials used for hydraulic shearing machine blades, along with the processing techniques involved.
Materials Used for Blades
- Tool Steel: High-quality tool steels such as D2 (SKD11), H13 (SKD61), and Cr12MoV are often used for their high hardness, toughness, and resistance to abrasion. These steels maintain their sharp edges even under high-stress cutting conditions.
- Carbide Tipped Blades: Preferred for cutting harder materials or applications requiring extended blade life. Carbide tips provide enhanced cutting performance and longevity.
- High-Speed Steel (HSS): Known for their ability to withstand high temperatures and maintain hardness at elevated cutting speeds. Suitable for applications requiring high wear resistance.
Blade Processing Techniques
The manufacturing of hydraulic shearing machine blades involves several key processing techniques to ensure optimal performance:
- Heat Treatment: Blades undergo heat treatment processes such as quenching and tempering to achieve desired hardness and toughness.
- Precision Grinding: Ensures uniform blade thickness and edge geometry, critical for clean and accurate cuts.
- Surface Coatings: Some blades are coated with materials like titanium nitride (TiN) or chromium nitride (CrN) to improve wear resistance and reduce friction during cutting.
- Alignment and Balancing: Ensures smooth operation by minimizing vibration and ensuring consistent cutting performance.
Maintenance and Care
To maximize the lifespan and performance of hydraulic shearing machine blades, regular maintenance and proper care are essential:
- Lubrication: Ensure blades are adequately lubricated to reduce friction and heat generation during cutting.
- Inspection: Regularly inspect blades for signs of wear, chipping, or damage. Replace blades as necessary.
- Storage: Store blades in a clean, dry environment to prevent corrosion and maintain sharpness.
The selection of appropriate materials and the application of precise processing techniques are crucial in ensuring hydraulic shearing machine blades perform effectively and efficiently. By understanding the role of blade materials
Conclusion
Lorem ipsum dolor sit amet, consectetur adipiscing elit. Ut elit tellus, luctus nec ullamcorper mattis, pulvinar dapibus leo.